Carbon-neutral Plasma pyrolytic technology
Green Hydrogen – HTT plasma technology helps to solve two global crises: climate change and Environment pollution
We Offer Solutions Applicable to Carbon Neutrally Hydrogen Power including Zero Carbon Emission and High Purity Hydrogen Gas.
CARBON-NEUTRAL PLASMA-PYROLYTIC TECHNOLOGY FOR PROCESSING POLYMER WASTE
Hydrogen energy, as the most environmentally friendly process of transit of chemical energy into heat and electricity, is becoming more widespread in the modern world. However, the process of producing hydrogen on an industrial scale is associated with either significant emissions of carbon dioxide (CO2) (“blue hydrogen” obtained mainly from natural gas by steam reforming) or high energy costs (“green hydrogen” obtained by water electrolysis). At the same time, we must be aware that the cost of electricity during the electrolysis of water, in the end result, is also associated with carbon dioxide emissions, because only a small fraction of the world's electricity is currently produced without burning fossil fuels.
For thousands of years, humanity has received thermal energy (later turning it into mechanical and electrical energy) by burning natural fuels (wood, coal, oil, natural gas). Those. it was about the exothermic process of oxidation of carbon and hydrogen contained in natural fuel.
However, in the 21st century, the problem of reducing emissions of greenhouse gas, carbon dioxide, into the atmosphere has become acute. Because of this, the idea of separating the organic compounds of natural fuel into hydrogen and carbon has become attractive, so that later only hydrogen can be used for energy purposes, avoiding carbon oxidation, especially since carbon itself in its not oxidized form is a sought-after industrial raw material. Even more attractive to this idea is the fact that any organic waste, including organic polymer waste, which is becoming unacceptably large in the modern world, can be used as a feedstock for this process.
The binding energy of hydrogen and oxygen in a water molecule is more than 3 times higher than the binding energy of hydrogen and carbon in various organic compounds. Accordingly, it is much more profitable to obtain hydrogen from organic compounds from an energy point of view than from water. At the same time, by oxidizing a part (usually less than 50%) of the resulting hydrogen, we can make up for all the energy costs for the process of abstraction of hydrogen atoms from hydrocarbon compounds and make the process energy autonomous, which is fundamentally impossible in the process of abstraction of hydrogen atoms from water molecules.
The process of detachment of hydrogen atoms from organic molecules occurs already at temperatures of 1000 0C, and the intensity of this process increases sharply (according to an exponential law) with increasing temperature. Therefore, in the process of obtaining hydrogen from organic compounds, high-temperature (plasma) technologies become relevant.
Combined plasma-pyrolytic two-stage process for obtaining hydrogen from organic polymer waste.
At present, the technology of pyrolytic decomposition of organic polymer waste (mainly plastic waste and used tires) has become widespread. In such a process, polymers decompose in sealed pyrolytic reactors in an oxygen-free environment at temperatures of 500-800 C. Water vapor is most often used as a carrier gas in such reactors.
At the outlet of such a reactor, pyro gas of a complex hydrocarbon composition is obtained mixed with a carrier gas (steam) and a solid carbon residue mixed with some oxides that are initially present in polymers as modifying additives.
The mixture of pyro gas with water vapor is cooled and separated in several stages into hydrocarbon condensate, water and non-condensed hydrocarbon gas fraction, which is usually burned to obtain thermal energy necessary for the pyrolysis process. At the same time, about 500 kg of CO2 are emitted into the atmosphere for each ton of pyrolyzed polymer.
With this process, 32-38% of carbon black and 40-45% of heating oil (liquid hydrocarbon fraction of complex composition) are obtained from each unit of feedstock.
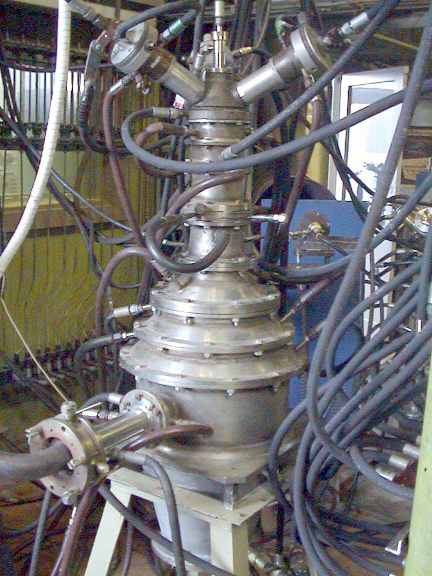
Experimental plasma reactor for producing hydrogen from gaseous and liquid hydrocarbon raw materials with a capacity of up to 100 Normal meter cubed per hour.